Save up to 30% off with these Memorial Day Deals - See Details
Valves

034 Motorsports .5mm Oversized Back Cut Intake Valve Audi | VW 4V
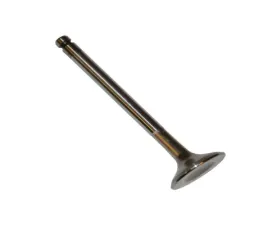
034 Motorsports 1.5mm Oversized Inconel Exhaust Valve Audi | VW 4V
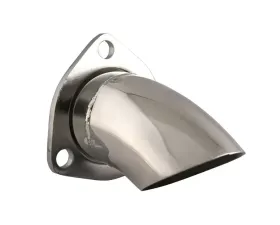
2.50 Inch Adjustable Stainless Steel Turn Down Quick Time Performance
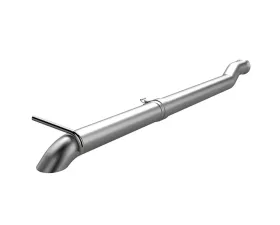
2007-2018 Jeep Wrangler JK 3.6/3.8L Crawler Eliminator Catback Exhaust Quick Time Performance
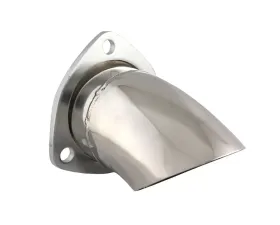
3.00 Inch Adjustable Stainless Steel Turn Down Quick Time Performance
Unlock Your Engine's Potential with High-Performance Valves from Vivid Racing
h2>Why Choose Vivid Racing for Your Performance Engine Parts?If you're looking to enhance your vehicle's performance, Vivid Racing is your go-to source for high-quality engine parts, including top-tier performance valves. With an extensive selection of renowned brands such as Ferrea, Brian Crower, and Supertech, we provide the best products tailored to meet the demands of automotive enthusiasts. Our commitment to quality and customer satisfaction sets us apart in the competitive landscape of high-performance automotive parts.
The Importance of Performance Valves in Engine Upgrades
When it comes to maximizing your engine's output, performance valves play a critical role. These components are designed to improve airflow, allowing your engine to breathe more efficiently. This results in increased horsepower and torque, making your vehicle not only faster but also more responsive. Whether you're racing on the track or simply want to enhance your daily driver, investing in high-performance valves is a decision that will pay dividends in performance and reliability.
Features and Benefits of Installing Performance Valves
Performance valves are engineered with precision and durability in mind. Made from high-quality materials, such as stainless steel and titanium, they are built to withstand the rigors of high RPMs and extreme temperatures. Here are some key features and benefits:
- Enhanced Airflow: Performance valves are designed with larger diameters and improved shapes to facilitate better airflow into and out of the combustion chamber, which is crucial for optimizing engine performance.
- Increased Durability: The materials used in performance valves are often more resilient than stock options, providing greater longevity and reliability under stress.
- Improved Engine Response: With better airflow and reduced restrictions, your engine will respond more quickly to throttle inputs, enhancing the overall driving experience.
- Custom Fitment: Many performance valves are designed to fit specific engine models, ensuring a seamless integration and optimal performance gains.
In conclusion, if you're serious about maximizing your vehicle's performance, look no further than Vivid Racing for your performance valves. Our extensive catalog of high-performance engine parts, combined with our dedication to customer service, ensures that you will find exactly what you need to take your driving experience to the next level. Don't settle for less; upgrade your engine with the best from Vivid Racing today!